This article further expounds on the paradigm established in the Post and Training Video B777 Engine Failure Analysis. The following resource material were drawn on for the contents.
- Airbus Flight Ops Brief : Handling Engine Malfunctions
- Flight Safety Foundation : Understanding Airplane Turbofan Engine Operation
- Rolls Royce : The Jet Engine Book.
- Boeing 777 FCOM/FCTM/QRH
- Other Airline specific sources.
Handling B777 Engine Malfunctions
The failure rate of the modern jet engine is at an all time low. The GE90 boasts an IFSD rate of one shut down per million+ operating hours. Most pilots will never see an actual engine malfunction – let alone a failure – in their career; hence all experience of this axiomatic checking/training event is from the simulator. Since simulators are not representative of the accelerations, noise and vibrations that many actual failures generate – your experience base can be miss-leading in terms of what you will actually encounter should your modern high-bypass fan engine malfunction.
Typically the following incorrect crew actions have been identified from a comprehensive review of engine malfunction related aviation incidents/accidents:
- Loss of Control (flight path/navigation not adopted in response to the engine malfunction)
- Rejected Takeoff above V1 (Startle Factor)
- Shutdown of the Wrong Engine
- Unnecessary Engine Shutdown
- Application of an incorrect procedure / deviation from published correct procedure
Primary Engine Parameters
Primary engine parameters commence with N1 (Fan Speed – GE) or EPR (Engine Pressure – RR) and EGT. N1/EPR is representative of engine thrust, and the following indications can be indicative of engine malfunction:
- Low N1/EPR can indicate an engine flameout
- Rapid fluctuating N1/EPR can indicate Engine Compressor Stall
EGT (Exhaust Gas Temperature) is measured after the final turbine stage of the engine outlet, and is a primary parameter for monitoring engine wear with time. While thrust setting on takeoff will be determined using a target N1/EPR value, as an engine wears over time the peak EGT during the takeoff roll will increase. High EGT can be an indication of:
- Engine Stall
- Tailpipe Fire
- Engine Fire
- Ageing Engine
Secondary Engine Parameters
Further engine parameters can be found on the lower MFD (Multi Function Display or the Compacted Engine Display on Upper EICAS. These include N2 (N3 for RR); Oil Pressure/Temperature/Quantity; and Engine Vibration.
- N2 (N3 RR) High Pressure Compressor Rotor Speed. Typically N2 (N3 RR) is used to monitor the engine start/relight sequence; the EEC’s use N2 (N3!) as a parameter to identify an engine that has dropped below idle. Rapidly fluctuating N2 (N3) can be indicative of an Engine Stall
- Oil Pressure, Temperature, Quantity. For GE engines the Oil Pressure and Temperature are measured prior to entry into the engine (RR also measures Oil Pressure entering the Engine Core; and Temperature leaving the Engine Core). Oil Pressure/Temperature have operating limits (Red Lines). There is no minimum Oil Quantity, although a quantity below a certain value will activate the inverse display of Oil Quantity as well as the automatic display of Secondary/Compacted Engine Indications.
- Fuel Flow. High Fuel Flow may indicate a Fuel Leak downstream of the Fuel Control Valve, particularly if rotor speeds are normal or low.
Engine rotor Vibration. Vibration is measured against all rotating cores (N1, N2, N3-RR) and in cases where the specific core causing vibration cannot be identified, an average broad band (BB) indication is given. While primarily used for condition monitoring, VIB can be useful to identify an engine after foreign object damage, or fan imbalance due icing. The level of vibration generated will be altered by engine speed. For a discussion of Engine Vibration malfunction handling also see P&T Engine VIB-ration.
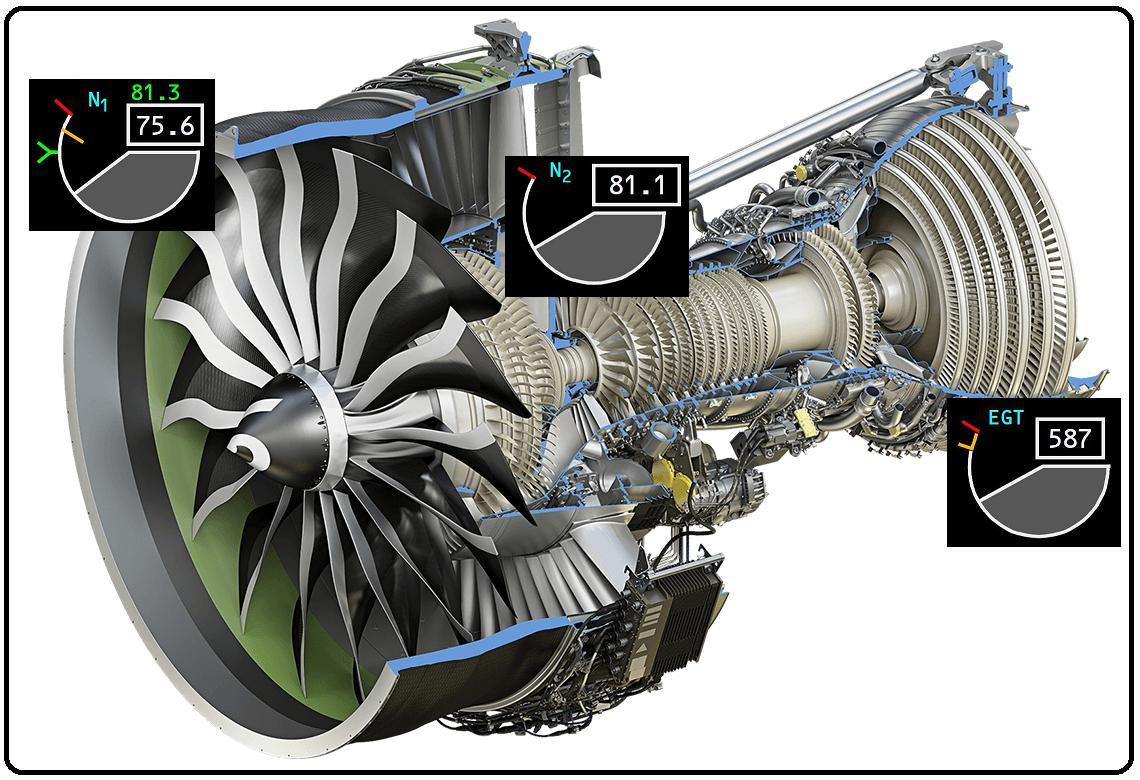
Identifying Engine Malfunctions
Many engine malfunctions can be identified thanks to specific warnings/cautions or engine parameter indications. However some malfunctions are harder to identify, or come in combination, and some flight crew knowledge is required to correctly identify the nature of the malfunction and the appropriate NNM procedure.
An engine fire (“External Fire” or “Nacelle Fire”) is fire in the engine where it’s not supposed to be – outside the combustion chamber – and is typically easy to identify with a dedicated EICAS [] FIRE ENG Warning / Fire Bell. Typical causes include inflammable fluids (Fuel, Oil, Hydraulic Fluid) coming into contact with very hot engine parts (Compressor, Turbine, Combustion Chamber Casing) – and can occur on the ground or in flight. Fluid contact can result from leaks, ruptures of lines and/or damage to engine components such as the accessory gearbox or combustion chamber.
Engine fire detection is determined by temperature sensing loops located in strategic areas around the engine and pylon. On the B777 each detector loop provides both Fire (Higher Temp, Warning) and Overheat (Less-Higher Temp, Caution) detection. Fire detection sensors are on two parallel loops and as long as both loops are functional, it requires both loops to detect a temperature anomaly before a Fire/Overheat Alert is generated.
The [] FIRE ENG procedure will:
- Shut Down the Engine;
- Isolate the Engine (Fuel, Hydraulic, Bleed Air, Electrical)
- Discharge the Fire Extinguisher
Crucially, there should always be adequate time to make your first priority “Fly The Plane” before attending to the fire. This applies whether carrying an engine fire into the air from V1; or commencing a drift down from high altitude – before commencing the fire fighting procedure. The longer the fire burns, the higher the likelihood of damage to the nacelle – but the first priority of the crew must be flight path and navigation – the safety of the aircraft.
As mentioned, the fire detection loops also serve as Engine Overheat detectors. Typically Engine Overheats are the result of heated airflow in areas of the engine not designed for it – potentially indicating some kind of engine damage resulting in high temperature compressor outlet airflow in the Nacelle.
The [] ENG OVERHEAT procedure attempts to eliminate bleed air and reduce thrust output on the affected engine in order to contain the overheat condition.
Tailpipe Fires will occur only on the ground, usually during engine start or shutdown and are a product of the excess fuel in the combustion/turbine/exhaust that ignites. Highly visible flame/smoke can be the result from the engine (Exhaust or Inlet).
While spectacular, Tailpipe Fires usually have very little impact on the engine itself, with any damage typically being constrained to the aircraft itself (lower wing surface, flaps, etc).
A Tailpipe Fire will NOT result in an engine fire warning on the flight deck – the only indication may be rising EGT (due any fire in the turbine area) and a highly excited ground engineer. Because Ground/Cabin/ATC rarely appreciate the difference – this is usually reported as an engine fire to the flight crew. If notified of an engine fire (on the ground) without accompanying flight deck indication, you should accomplish the [] Fire Eng Tailpipe procedure, which will:
- Shutdown the engine in order to halt fuel flow;
- Motor the engine to remove any remaining fuel.
Do not use the Engine Fire Switch. This will remove air supply to the engine and prevent the motoring procedure to remove any remaining excess fuel – the only effective crew action of fighting a tailpipe fire.
Do not use the Engine Fire Extinguishers. These discharge outside the engine core, in parts of the engine that are not affected by a tailpipe fire.
The [] Fire Eng Tailpipe procedure should be sufficient to stop the fire. The intervention of fire services should therefore be a last resort (such as if no bleed air is available to motor the engine) – because ground fire extinguishing agent can cause significant corrosive damage. Precautionary or Emergency Evacuations are generally not warranted for a Tailpipe Fire.
Low Oil Quantity alone is not a symptom of an engine malfunction requiring precautionary shut down or rejected takeoff. While there is no minimum (limitation) oil quantity on the 777, low quantity causes automatic display of secondary engine indications with a reverse display of the affected (low) oil quantity value. On the other hand, Low Oil Pressure or High Oil Temperature are signs of imminent engine failure and the [] ENG OIL PRESS or [] ENG OIL TEMP checklists must be actioned.
For an engine flameout ([] ENG FAIL) the combustion process has stopped. This can be for a variety of reasons, such as:
- Fuel Starvation
- Airflow Starvation (such as Volcanic Ash)
- Heavy Rain/Hail/Icing
- Engine Stall
- Engine Control System Malfunctions
Potentially, flight at high speed and low engine thrust through heavy rain or hail increases the risk of engine flameout. While the Start/Ignition Selector offers a CON selection (continuous ignition) – there is no Normal or Non-Normal Procedural Step that requires this selection.
Engine flameout protection is provided by the EECs through auto-relight which is activated when an engine is below a minimum idle value with the Fuel Control Switch in Run. In such an occurrence, both ignitors are activated, and fuel flow is scheduled appropriate to the engine (re-light) conditions. If the engine does not recover and runs down below a minimum idle value, the EEC shuts off fuel and ignition and disables the auto–relight function. The EICAS caution message ENG FAIL (L or R) is displayed if an engine unexpectedly decelerates to less than idle speed.
An engine flameout is detected by a rapid decrease in EGT, N2 (N3 on RR engines), Fuel Flow, and N1.
The ubiquitous Engine Limit Surge Stall Left/Right Checklist catches an array of engine non-normal events, staring with Limit Exceedances.
EGT Exceedance
The EGT red line is the only EICAS limit that can be occasionally exceeded without direct operational impact or damage to the engine.
The EGT reaches a peak at the end of the takeoff roll, close to rotation or just after liftoff due to thermal inertia of the engine. The difference between the Takeoff EGT Limit (red line) and the peak EGT during takeoff is called the EGT margin, and while directly affected by thrust output (as a percentage of TOGA), ambient temperature, etc – this margin reduces as the engine gets older. A less efficient engine burns more fuel to produce the required thrust, resulting in higher EGTs on takeoff.
The engine may exceed the EGT Limit without any failure and will continue to deliver thrust. As such, if you notice an EGT exceedance during takeoff, the takeoff should bee continued and established in initial climb, before applying the [] Eng Lim/Surge/Stall memory items. EGT exceedances are to be recorded in the Technical Log.
Note that if EGT suddenly increases when setting takeoff thrust – it is most likely the symptom of a severe engine failure.
Engine rotor speed exceedances are the result of an engine malfunction. The [] Eng Lim/Surge/Stall memory items will reduce thrust until the indication is below limits, or shut the engine down if operation below limits is not possible.
Engine Vibration (EICAS VIB)
The causes of Engine Vibration include:
Engine Rotor Imbalance
- Birdstrike / FOD causing blade deformation
- Compressor Blade loss/damage
- Icing build up on Fan/Stator Vanes
The B777 airborne vibration monitoring system is intended for condition monitoring – but is a useful tool for isolating engine anomalies. There is no certified vibration limit, nor any crew procedures as a direct result of EICAS vibration indications.
High N1 vibration will most likely be accompanied by tactile (airframe) vibration as well – this may not be the case for N2 (N3). Any rotor vibration may be accompanied by anomalies in other parameters and will usually respond to thrust lever adjustment. As a general recommendation:
- Crosscheck other engine parameters (N1, N2, EGT, Oil Pressure …) with the other engine
- Reduce thrust on the affected engine below advisory indication levels if flight conditions permit (as per [] Eng Lim/Surge/Stall)
Sudden increases in vibration level could indicate deterioration of the engine. Vibration alone should not lead to an in-flight shut down – see P&T Engine VIB-ration
Engine Surge/Stall
Engine Stall (Surge) is essentially a stall of one (Stall) or all (Surge) of the Compressor section(s), caused by:
- Engine deterioration
- FOD ingestion (Bird) or Ice
- Engine Bleed System Malfunction
- Other Engine System Malfunction (Fuel Scheduling, EEC Surge Protection, etc)
Jet engine compression is achieved aerodynamically through the various stages of the compressor(s). If air flowing over a compressor blade stalls, airflow is disrupted and the compressor can no longer compress the incoming airflow. Flow reversals can result, resulting in immediate and significant thrust loss. Engine Stall is characterised by:
- One or more loud bangs;
- Instant loss of thrust, resulting in Yaw
- Engine parameter (N1, N2, N2, EP) variations and EGT increase
- Visible flames from the inlet and/or tailpipe
Engine Stall on Takeoff
Flight crew reports of actual engine stall events on takeoff confirm that the bang is much louder than any noise previously heard on the flight deck (or simulator). Because of the noise and yaw movement of an engine stall, the event can be incorrectly identified as a tire burst or an explosive device. The Startle Factor associated with an Engine Stall on takeoff may lead to rejecting the takeoff above V1, causing a runway overrun. Boeing/FAA have a training video on Stall Engines (click the image to the right, sorry for the low-res).
“The compressor stall I had on the 777-300ER early on take off was a very aggressive and loud manoeuvre. My initial reaction was that we had hit another aircraft; it felt like the landing gear bogie had run over a very large object. The nose wheel lifted and pointed us toward some 30 degrees from the runway centre line. However the simulator gives you the impression that a stall is very difficult to identify. You hear a faint “Popping” noise and a slight yaw. On a scale of 1-to-10 with 10 being what a real event feels like then the sim is a 3.”
At low power (such as thrust reduction at top of descent) – the engine stall is characterised by:
- One or more muffled bangs
- Engine Vibration
- Engine Parameter fluctuations and increases in EGT
Engine stall can result in high EGT – including over limit occurrences – because airflow into the combustion chamber is compromised by the compressor stall and is not enough to ensure turbine cooling, even as fuel flow is scheduled for higher anticipated airflow. Engine stalls are harder to detect at low power.
Engine Stall can be:
- Recoverable without Crew Action
- Recoverable with Crew (or EEC) Action
- Not Recoverable
Recoverable Stall without Crew Action
One or more loud bangs may be heard; associated engine parameters fluctuate but quickly return to normal. In most occurrences, the parameters are back to normal when the flight crew focus turns to the engine parameters, which can make it difficult to determine which engine has the malfunction. Engine operation can be checked by smoothly moving the thrust levers one at a time to check engine response and stall-free operation.
Recoverable Stall with Crew/EEC Action
Engine Stall indications (noise, parameter fluctuations, etc) continue until the crew reduce thrust in accordance with the [] Eng Lim/Surge/Stall memory items. Alternatively the stall may be resolved through EEC action – the EEC will change fuel scheduling to unload compressor internal pressure. If the stall indications disappear with thrust reduction the crew can advance thrust slowly as long as the stall does not re-occur. The engine must be kept below the level at which engine stall occurs.
Non-Recoverable Engine Stall
After the initial Stall Indications (noise, parameter fluctuations, etc) the engine will decelerate to zero power as if fuel has been cut off. Crew Procedures will reduce engine thrust levers to idle and shut down the engine.
A non-recoverable stall can be accompanied by severe engine damage if it is not identified and correct by flight crew – and may lead to an engine failure.
The actual cause of compressor surge can be complex and may not result from severe engine damage. A single compressor stall is unlikely to cause severe engine damage, but sustained surging will eventually overheat the turbine because of compromised airflow in relation to the fuel being scheduled. Compressor blades may also be damaged as the result of repeated violent surges – this will rapidly result in an engine that cannot be sustained at any power setting.
For unexplained momentary Engine Surge/Stall (where the engine fully recovers) during takeoff, climb or during and EDTO sector – the decision to continue should be made in concert with Operations. When a cause cannot be found for even a momentary engine malfunction – the risk profile of EDTO operations is altered significantly. While local factors such as icing or heavy rain can be considered relevant to your deliberations – the root cause of an event can only be determined after trouble shooting or a Boroscope carried out on the ground.
Loss of Engine Thrust Control
Even the 777 with it’s full authority digital engine controls are subject to this malfunction, both on the ground and in the air. Often the major challenge faced by the crew is recognising the condition and correctly determining which engine has malfunctioned.
Failures affecting engine, fuel control, thrust control/position feedback have caused a loss of thrust control. In the simulator the thrust lever failure typically comes in three flavours
- Thrust Lever Signal Loss – EEC’s command idle thrust
- Thrust Lever Signal Channel Failure – EEC’s will not reduce thrust below fail point
- Engine Shut Down
In all cases the affected engine does not respond to thrust lever management.
Depending on the failure, control loss may not be immediately obvious since many engines fail at a fixed thrust setting or thrust lever position. Since recognition can be difficult, if a loss of engine control is suspected – continue the takeoff or remain airborne until the [] Eng Lim/Surge/Stall checklist can be accomplished.
In some conditions, such as during low speed (high thrust) ground operations, immediate engine shutdown might be required to maintain directional control.
Severe Engine Damage can be a challenge to clearly define. While the checklist condition statement seems pretty straight forward – it’s important to appreciate that severe engine damaged may also be accompanied by symptoms such as:
- Fire Warning
- Overheat Warning (from leaked hot air)
- Engine Surge/Stall (damaged compressor blades)
The symptoms of severe engine damage will be similar to Surge without Recovery – loud noise; rapidly reducing engine rotor (N1, N2, N3) speeds; reducing fuel flow. EGT may raise momentarily – and there will be a loss of power.
As always the initial task of the crew is not to identify the specific nature of the failure/fire – but to Fly The Plane. Only once the flight path and navigation is stabilised should the crew diagnose the malfunction.
Engine Seizure
Engine Seizure is where one (or more) of the engine rotors cease to turn in flight, potentially suddenly. In practice, this is tends to occur at low rotor speeds after an engine shutdown as the static and rotating components lock up against each other. This virtually never occurs in flight for the N1 – the Fan has too much inertia and is driven by ram air too forcefully to be stopped by the static structures in the engine. That said – if the N1/Fan does seize there will be perceptible drag for which the Flight Crew will need to trim for – as opposed to a seized N2 (or N3).
Only a (very) severe engine damage will cause a seizure, to the point where the compressor/turbine sections are mostly destroyed. This is unlikely to be an instantaneous process. Symptoms include vibration, zero rotor speed, yaw, possibly unusual noises.
Engine Separation
Engine separation is an extremely rare event, accompanied by the loss of all primary and secondary engine parameters, noises, yaw, etc. Separation is most likely to occur during takeoff/climb or during the landing roll and aircraft handling is likely to be affected. The use of the Engine Fire Switch is crucial to close the fuel spar valve and prevent a significant fuel leak.
In the simulator – it’s pretty hard to miss, or miss-identify.
So … Which Checklist?
In the event of [] ENG FAIL on EICAS – as long as there is no Airframe Vibration (or any airframe vibration that occurred during the initial malfunction does not continue after engine shutdown – the engine can be considered as Failed (Engine Speed Below Idle) and no memory items are applicable. Similarly, if an engine has malfunction and failed in such a way as to result in engine damage (including seizure during the shutdown or a limitation exceedance during the initial malfunction) – only the [] ENG FAIL checklist is required. In principle, this action is completely in line with the QRH Condition Statements and Non-Normal Checklists.
That said – in the event of an engine malfunction it is the responsibility of the Aircraft Commander to choose the course of action he/she believes to be appropriate to the specific situation. It is very likely that a severely damaged engine with/without rotor seizure that even after shutdown there could be ongoing airframe vibration – leading to [] Eng Svr Damage/Sep memory items.
For further exploration of this paradigm and associated Infinidim Training Video – see B777 Engine Failure Analysis.
Carefully assess the need to re-light an engine in-flight. Consider seeking Engineering guidance (if appropriate) prior to considering an engine re-light. That said – final responsibility to re-start an engine in flight after an in-flight shutdown remains with the Captain/Pilot in Command.
Factors to consider include:
- It’s glib, but not untrue that (these days) – Engines do not fail without cause. Our engines have re-light capability and so it could be said that the EECs will already have tried to re-start the engine during the initial failure sequence. As such further attempts to re-light are unlikely to be successful.
- It is highly unlikely that Engineering can access real-time data from the malfunctioning engine, nor respond to any down-linked reports sent automatically during the malfunction in real time. Further, any such reports may require referral to engine manufacturer specialists before any meaningful feedback can be obtained.
The QRH [] Eng In-Flight Start and [] ENG FAIL require you to have a need to re-start an engine that has malfunction and been shut down. While still somewhat subjective – it’s an improvement from what the checklist(s) used to say (which was “Restart is desired :“) !!
Additional Information
If you are not sure which Engine is malfunctioning – keep it running. By implication, if you are not sure which engine has the problem, then it’s probably delivering meaningful thrust, at least for the time being.
Several accidents have been caused by a rushed decision to shutdown (usually from memory) the wrong engine when the indications were not immediately clear. The No/Abnormal Response to Thrust Lever scenario in particular can lead to confusion on the flight deck as to which engine is malfunctioning – slow down, fly the aircraft, analyse the failure.
If instrumentation is insufficient to clearly identify the malfunctioning engine – smoothly moving the thrust lever and checking for appropriate response through changes in engine parameters should assist.
Tailpipe Fire Incidents
(Thanks Alex!)
Questions
Ken.
If you find my content useful and are in a position to do so – I would appreciate a contribution to my PayPal account (ken.pascoe@gmail.com) – If you use the Friends and Family feature in PayPal it reduces the charges to the transfer. Please note that when sending money in this way you are removing any form of purchase protection, which is not relevant to a contribution of this type anyway.